Background
Humankind depends on a healthy global ocean. Whether coastal or inland, all communities are affected by changes in ocean processes that impact weather and climate. The ocean is essential to food and economic security for coastal communities in addition to serving as both a source of inspiration and a cultural touchstone for many societies. While human needs are predicated on ocean health, many of the tools used to study, explore, and understand the ocean are inaccessible to the vast majority of ocean stakeholders (Harden-Davies et al., 2022). This is due in part to the prohibitive costs of even the most basic oceanographic equipment (Bennett et al., 2021). Financial barriers limit the scope and breadth of ocean observation and suppress the diversity of knowledge seekers working to address problems facing the ocean (Lauro et al., 2014). One approach to moving toward global parity in ocean research is the development and application of accessible, low-cost, open-source instrumentation—in particular, the workhorse of all oceanographic research, the CTD.
A CTD is a device that provides salinity (conductivity), temperature, and depth measurements in the ocean, knowledge that is needed to unlock patterns hidden beneath the waves, detect changes in their local waters, and establish environmental baselines. CTD data are essential in a variety of marine scientific applications. CTDs are used to identify temperature and salinity anomalies (Dickson et al., 1988), quantify salt- and freshwater admixture and stratification in estuarine systems (Cloern et al., 2017), and identify and track ocean currents (Johnson et al., 2002). CTDs can also be used to detect the heat signatures of hydrothermal vents (Connelly et al., 2012), create sound velocity profiles for calibrating sonar (Grekov et al., 2021), and aid in the acoustic tracking of fish and other ocean wildlife (Roquet et al., 2017). Additionally, CTD casts can be helpful in finding undocumented wastewater discharges (DiGiacomo et al., 2004), identifying suitable regions for aquaculture (Longdill et al., 2008), detecting saltwater inundation in aquifers (Cantelon et al., 2022), and assessing changes following intense storms or heavy rains (Li et al., 2009). CTD casts were used to establish the depth of the Challenger Deep and assess thermo- and haloclines within the Mariana Trench (Taira et al., 2005). Importantly, CTDs provide critical measurements to better understand the impacts of climate change (Abraham et al., 2013).
Even the most inexpensive commercial CTDs can cost several thousand dollars and require expensive maintenance and calibration services. Some also require proprietary software and analytics packages, though free and low-cost alternatives may exist. The cost and complexity of a CTD impedes the progress of researchers working with limited budgets, including scientists from emerging economies, private citizens, environmental educators, conservation and management practitioners, and students of all levels interested in understanding their local waterways. To help reduce this barrier, we developed the OpenCTD, a low-cost, open-source alternative to the traditional CTD. Designed to be built by the end-user from relatively accessible materials, the OpenCTD provides access to this oceanographic tool as well as the skills to maintain, calibrate, deploy, repair, and replace it. This promotes data independence and local ownership of the means of knowledge production, allowing knowledge seekers to pursue their own lines of inquiry, independent of institutional support and the ephemeral nature of conservation funding.
The OpenCTD is intended for knowledge seekers working in nearshore coastal ecosystems where entire research projects can be conducted for less than the cost of a single commercial CTD. Its 140 m depth limit covers the majority of the world’s continental shelves (Harris and Macmillan-Lawler, 2016). The OpenCTD is designed with three core principles in mind:
• Low Cost. By focusing on the most inexpensive components that can maintain reasonable data quality, the cost of the OpenCTD, excluding consumables, can be reduced to approximately $370 and two to three days of labor.
• Accessible. Components have been carefully selected so that they may be easily sourced from electronics distributors, chain hardware stores, and large online retailers with global distribution channels. The use of bespoke components has been minimized. The OpenCTD uses the Arduino integrated development environment (IDE), an open-source hardware and software ecosystem with a robust user community.
• Open. By encouraging transparency, access, and community collaboration through an open-source approach, knowledge seekers can use, adapt, and modify the hardware and software to suit their needs (Perens, 1998). In the hands of active and engaged communities, open-source approaches can facilitate the rapid development, diversification, and distribution of new tools. All firmware and hardware schematics are released under an MIT Open Source License (Ballhausen, 2019).
Climate change has created an urgent need for extensive, high-resolution measurements of oceanographic conditions both globally and locally (Malone et al., 2010). At the same time, government funding at both local and federal levels for climate change research can be unreliable. Low-cost alternatives to common scientific instruments stretch the impact of extant funding and allow a wider range of ocean knowledge seekers, including environmental monitoring programs, community groups, nongovernmental organizations, and concerned individuals, to contribute water-quality measurements. By increasing access to the tools of ocean science for a broad cohort of ocean knowledge seekers, the OpenCTD encourages a community-up model of environmental monitoring, whereby inquiry is driven by individual and group curiosity rather than the priorities of major funders, a phenomenon that can be broadly described as marine citizen science or community oceanography (Sandahl and Tøttrup, 2020; Lin Hunter et al., 2023).
In declaring the 2020s the Decade of the Ocean, the United Nations set the explicit goal of promoting a transparent and accessible ocean “whereby all nations, stakeholders, and citizens have access to ocean data and information technologies and the capacities to inform their decisions” (Ryabinin et al., 2019). As we approach the mid-point of the UN Decade of the Ocean, the OpenCTD can help ensure not only that the products of ocean research are available to “all nations, stakeholders, and citizens” but also that the tools to produce that knowledge are available to all, as well.
Materials and Cost
The OpenCTD is controlled by the Adafruit Adalogger M0 Arduino microcontroller, which is equipped with an integrated microSD card reader. This microcontroller interfaces with an array of five sensors: three DS18B20 digital temperature sensors, an Atlas Scientific EZO conductivity circuit with a K 1.0 conductivity probe, and an MS5803-14BA 14-bar pressure sensor. A DS3231 precision real-time clock records date and time. The device is powered by a 3.7 V lithium-ion polymer battery, and the electronics are housed in a 2-inch schedule-40 PVC pipe sealed with epoxy on one end and capped with a standard plumber’s test cap, which allows access to the electronics while creating a watertight seal (Figure 1).
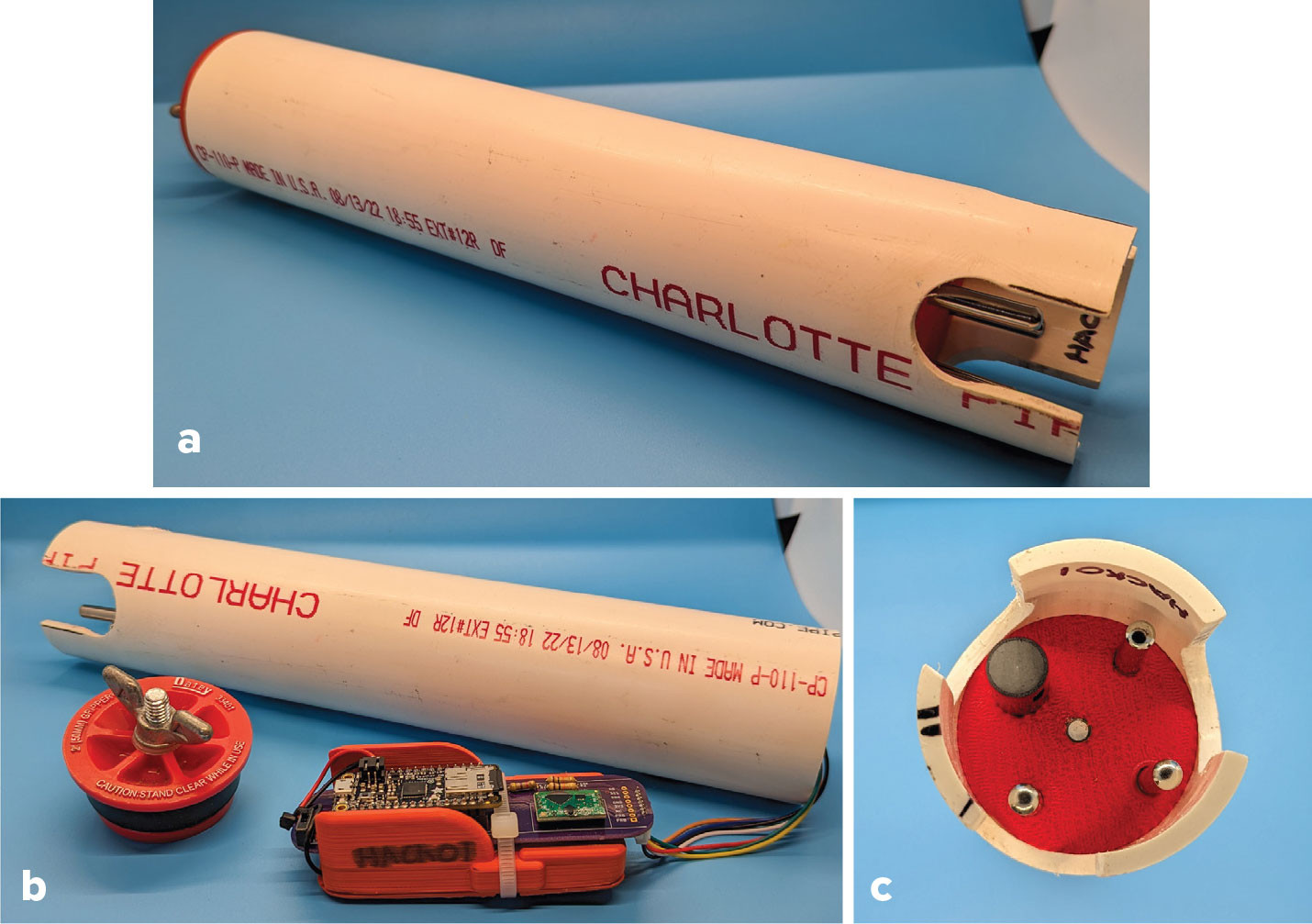
FIGURE 1. The OpenCTD. (a) The assembled and sealed OpenCTD ready for deployment. (b) The OpenCTD with plumber’s test cap removed and control unit showing Arduino microcontroller, Atlas EZO conductivity circuit, wiring harness, and 3D-printed chassis protecting the battery and other electronics. (c) Head-on view of the sensor array with pressure sensor (white circle in the middle of the unit), conductivity probe (large black probe), and temperature probes (three stainless steel rods). > High res figure
|
The cost of construction is dependent on local supply chains, but within the United States, the OpenCTD can be constructed for approximately $370, excluding tools and consumables (Table 1). That cost can be reduced to less than $300 with the sourcing of alternative sensors and components. Consumables add approximately $40 to $90 to the assembled costs, depending on sourcing and availability. A basic electronics fabrication lab with the tools necessary to construct OpenCTDs can be outfitted for approximately $350. This enables ocean knowledge seekers to establish their own OpenCTD fabrication and maintenance program for less than $1,000 USD (Table 1).
TABLE 1. Abbreviated list of materials costs for the OpenCTD. Full details, bill of material, and sourcing guide provided in the online supplementary materials. Costs are based on most recent supplier quotes and are current as of June 2022, excluding local taxes and shipping. > High res table
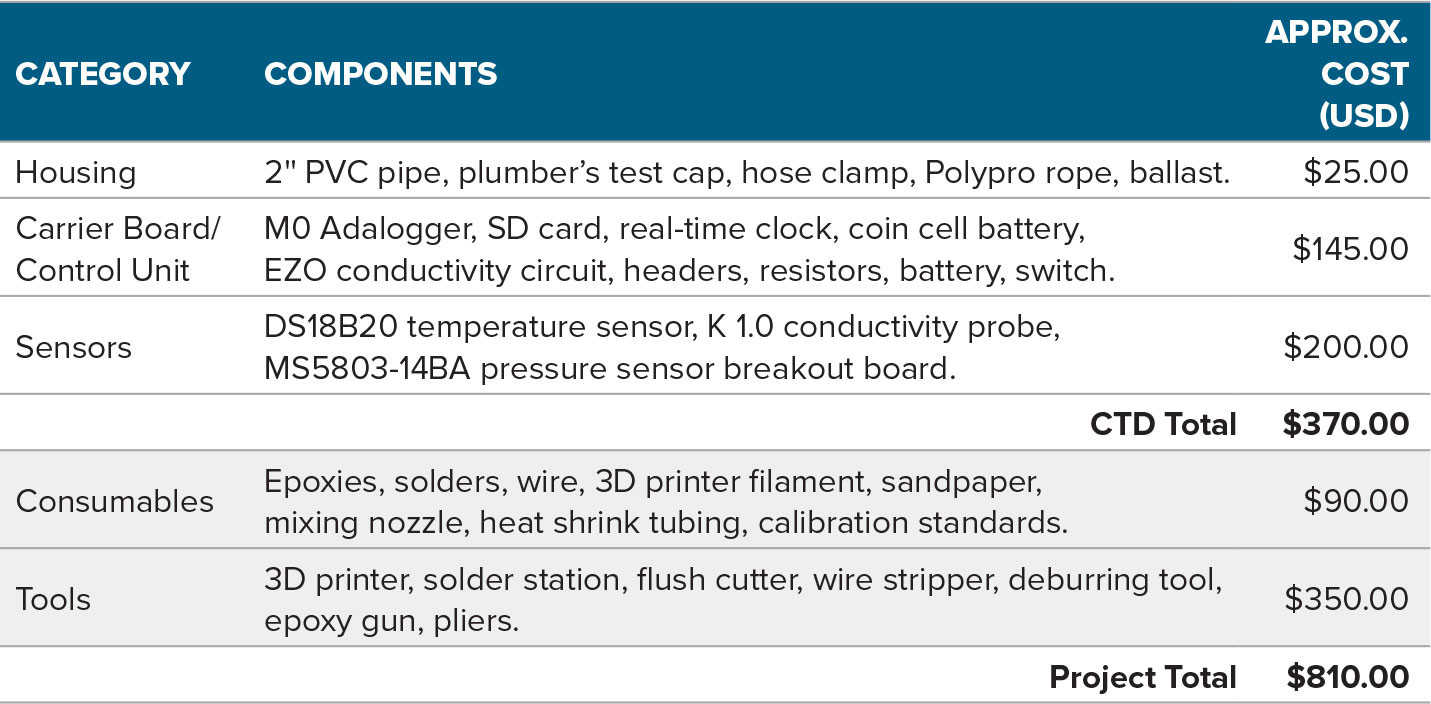
|
Assembly
Construction of the OpenCTD occurs in three phases: assembling the control unit, assembling the sensor package, and housing the electronics. The control unit is either a custom printed circuit board (PCB) or a standard prototyping board populated with a real-time clock, a conductivity circuit, and a microcontroller. The custom PCB dramatically reduces the complexity of the build. Anticipating that not all users will have access to custom circuit boards, an alternative build pathway using exclusively off-the-shelf components and a 3D-printable chassis was also developed. These two build pathways ensure that the OpenCTD remains as widely accessible to users as is reasonably possible. After nearly a decade of experimentation and testing, we have determined that the Atlas EZO conductivity circuit, although not in itself an open-source component, stands apart as both the least expensive and most accessible option for measuring salinity in seawater.
The sensor package is comprised of three temperature sensors, one pressure sensor, and one conductivity probe. The pressure sensor is assembled separately and potted in a 3D-printable sensor template with 2-ton marine epoxy. The conductivity probe and temperature sensors are off-the-shelf components and require only small modifications to their wiring. All five sensors are connected to a wiring harness that interfaces with the control unit. Sensors are seated in the PVC pipe using a 3D-printed template and potted in high-shear-strength marine-grade epoxy, resulting in a watertight passthrough for the five sensors. Depending on the needs and preferences of the user, the battery can be either incorporated into the control unit with an internal switch or built into the housing with an external magnetic switch.
The OpenCTD can be built over two days by relatively inexperienced users. Several alternative build pathways exist that allow the user more control over parts sourcing. An alternative control unit can be assembled from less expensive off-the-shelf components rather than the custom PCB. An alternative pressure sensor can be assembled from the raw board-mounted pressure chip, resulting in a substantial cost reduction over the prefabricated breakout board, but requiring more sophisticated soldering. Supported alternative configurations include a deep pressure module and a higher precision temperature probe.
Access to the electronics is possible using a standard 2-inch plumber’s test cap that has been pressure tested both in the field and in a barometric chamber to 140 m. Data are stored as a CSV (comma-separated variables) file and downloaded manually from the SD card following deployment.
Comprehensive assembly instructions are provided in the OpenCTD: Construction and Operation Manual (see online supplementary materials; Thaler et al., 2020). The most up-to-date version of the build guide can be found in the OpenCTD GitHub repository (Table 2).
Firmware, Shapefiles, and PCB Design
The firmware for the OpenCTD is written in the Arduino programming language (Dunbar, 2020). This language shares similarities with C and uses an open-source IDE. The Arduino platform has been designed with both open-source development and STEM education programs in mind. It is ideal for lower power applications like the OpenCTD that do not require the processing capacity of an integrated single-board computer like the Raspberry Pi. Arduino-based systems are also broadly available, and numerous localized variants exist.
All source code, platform forks, and support firmware for testing, calibration procedures, and troubleshooting are available through the OpenCTD GitHub repository (Table 2). Shapefiles for 3D-printed components as well as schematics and Gerber formatted manufacturing files for the OpenCTD Custom Carrier Board are also available in the GitHub repository.
Calibration and Data Quality
Precise calibration is critical to the successful operation of an OpenCTD. The MS5803-14BA pressure sensor outputs absolute pressure at 0.2 mbar resolution, allowing for sub-centimeter depth measurements. The pressure sensor is factory calibrated, requiring no additional input from the user. Testing of numerous pressure sensor modules both directly from the chip manufacturer and from third-party integrators that manufacture breakout boards has revealed less than 1% deviation across sensors. Response time for the MS5803-14BA is 8.22 milliseconds, as per manufacturer’s specifications (Table 3).
The DS18B20 digital thermometers used for measuring temperature have an advertised accuracy of ±0.5°C. To mitigate the inherent limitations of low-cost temperature sensors, the OpenCTD integrates simultaneous measurements from three sensors. Though mathematically, by taking an average of three sensors, we should expect an uncertainty of ±0.29°C, experimentally, OpenCTD has an observed accuracy of ±0.1°C with a consistent linear offset that can be determined by comparing the slope produced by taking the average of the three sensors across multiple temperature measurements against a known temperature probe. Response time for the DS18B20 sensors varies with the quality and mass of the cladding and epoxy potting. The thermal time constant (the time it takes for a temperature sensor to cool to 63.2% of the total difference between a stable high temperature and a stable low temperature) for the temperature sensors was determined experimentally for DS18B20 thermistors in a variety of different claddings from different manufacturers and found to range from 5.7 to 8.5 seconds (Table 3).
The conductivity probe requires direct calibration against known salinity standard solutions using a protocol detailed in the Construction and Operation Manual (see online supplementary materials). When properly calibrated, the error rate for the K 1.0 Atlas Scientific EZO conductivity sensor in standard seawater is less than 1%, with a 90% response time of 1 second, as per manufacturer’s specifications (Table 3).
The OpenCTD Construction and Operation Manual provides a detailed description of the procedure for calibrating the temperature, pressure, and conductivity sensors, with a focus on the conductivity sensors and the step-by-step process necessary to ensure accurate salinity readings (see online supplementary materials). A thermally stable environment is established using an inexpensive foam cooler and the heating element from a 3D printer. Sensors are then calibrated against two known conductivity standard solutions. Firmware to facilitate easy calibration of the instrument and a standalone calibration guide is also available on the OpenCTD GitHub repository (Table 1).
While pressure and temperature remain stable throughout the lifetime of the sensor, conductivity needs to be calibrated periodically in order to ensure that the instrument is returning accurate water quality data. We tested a series of different calibration protocols for the OpenCTD, including the recommended calibration protocol outlined in the Construction and Operation Manual; a protocol designed to minimize waste in scenarios where access to reliable salinity standards is limited, as described in the calibration section of the build guide; and a temperature compensated protocol for scenarios where maintaining a controlled temperature environment may not be possible (Figure 2). Conductivity readings from the recommended protocol remained within 5% relative to a Thermo Orion commercial conductivity sensor across the whole range of readings. To help determine how long the OpenCTD holds calibration, we tested three instruments, all calibrated using the same recommended calibration protocol, including an OpenCTD that had been calibrated 18 months prior to the test and deployed dozens of times in the North Atlantic, an OpenCTD built new for this study and calibrated on the day of the test, and an OpenCTD used in Chesapeake Bay and calibrated six months prior to the test (Figure 3). Readings from all three instruments remained within 5% relative to the commercial conductivity sensor. In terms of salinity, the recommended calibration protocol deviated by an average of 0.35 PSU relative to the commercial conductivity probe across the entire salinity range, with a peak deviation of 1.02 PSU at the mid-range between the two calibration standards.
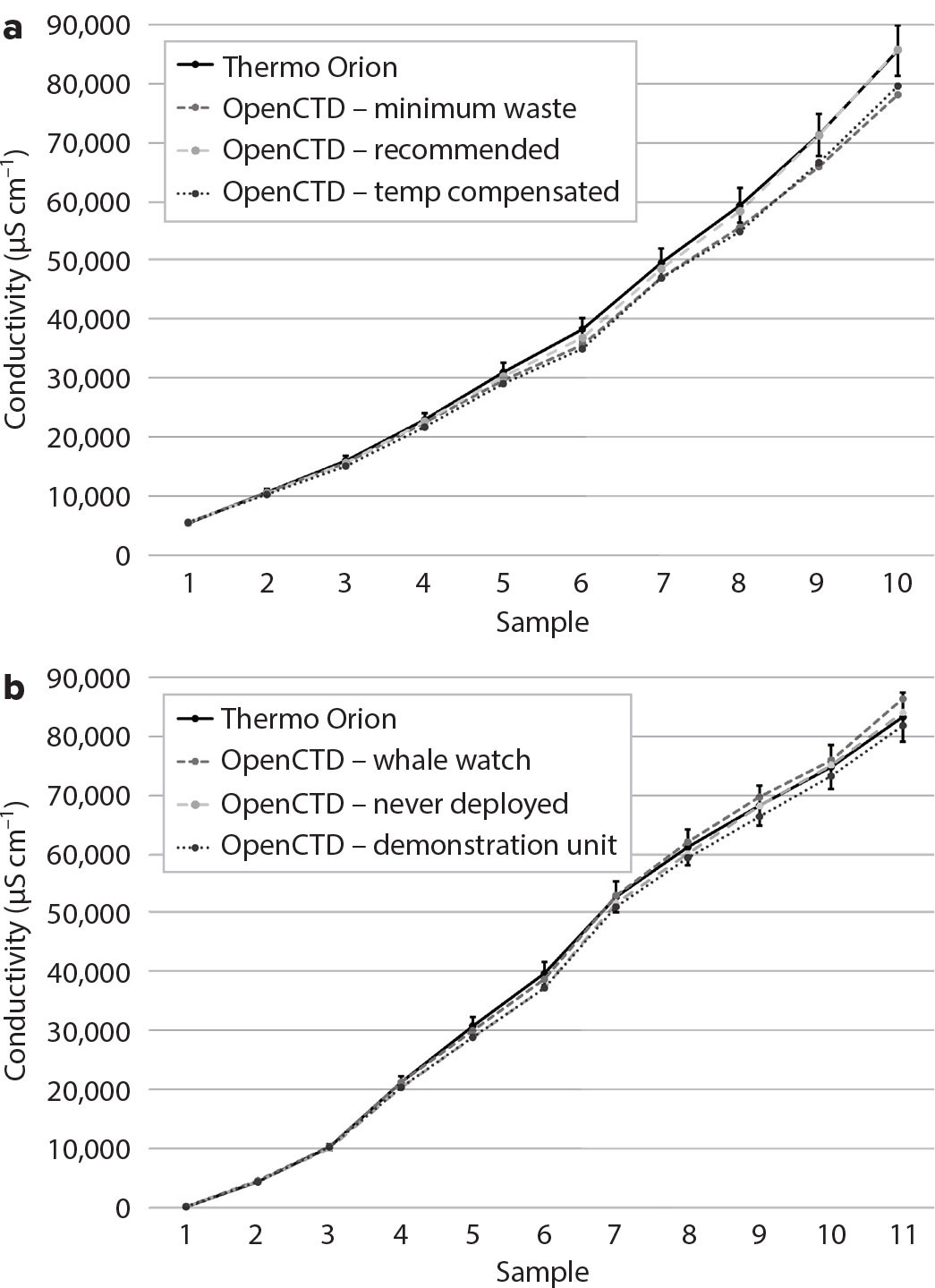
FIGURE 2. Comparisons between OpenCTDs and a professionally calibrated Thermo Orion Star A329. (a) OpenCTD calibrated under a variety of different protocols, including a protocol designed to minimize waste in scenarios where access to reliable salinity standards is limited, the recommended calibration protocol outlined in the manual, and the temperature compensated protocol for scenarios where maintaining a controlled temperature environment may not be possible. (b) Three OpenCTDs calibrated using the standard protocol at different times and used under different conditions, including one used for the New England Whale Watch Program calibrated 18 months prior to the test and deployed dozens of times near Bar Harbor, Maine; one built new for this study and calibrated on the day of the test; and one used locally for demonstrations calibrated six months prior to the test. > High res figure
|
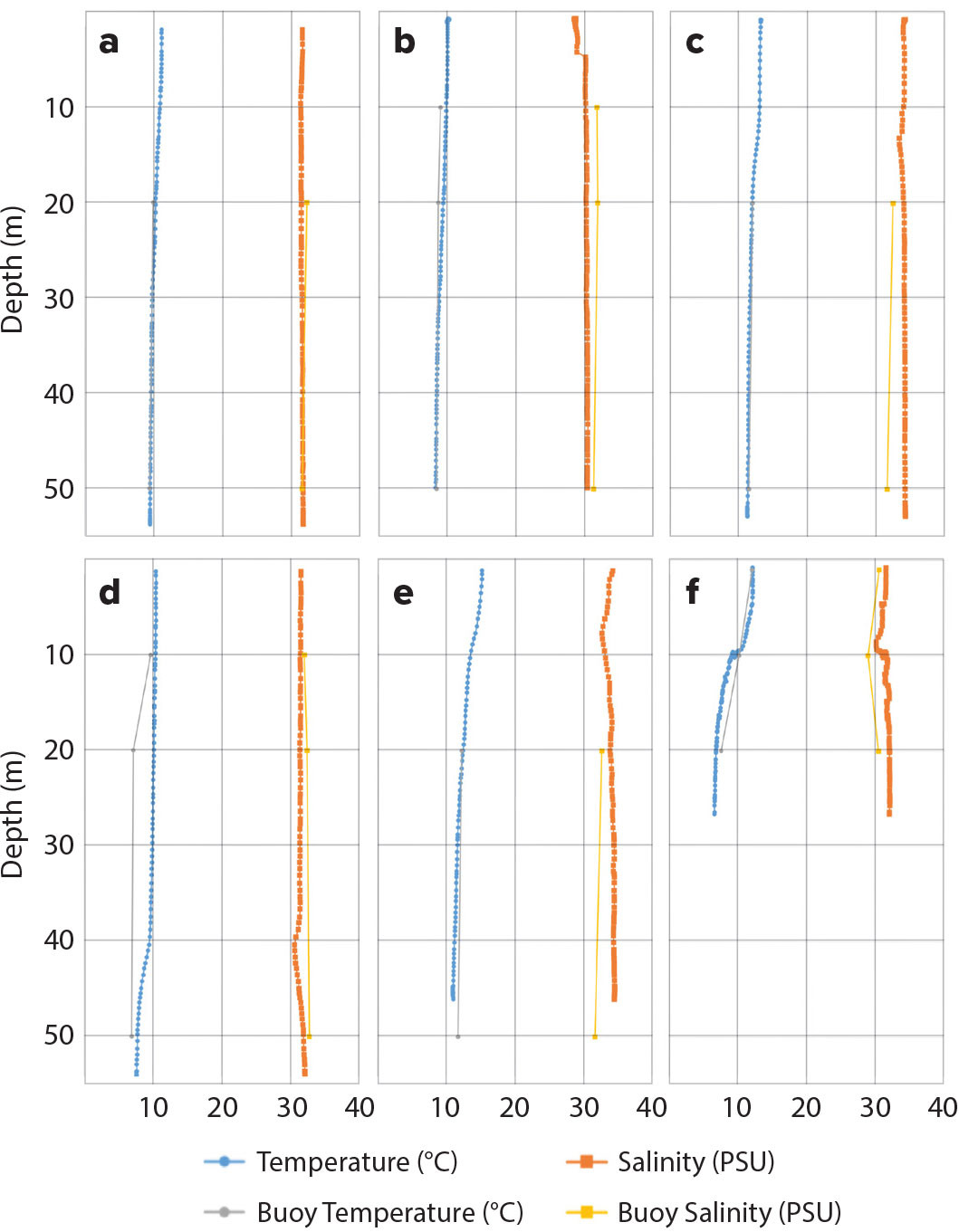
FIGURE 3. Representative sample of OpenCTD casts during the Community Oceanography While Watching Whales program, superimposed with temperature and salinity data from the nearest Northeastern Regional Association of Coastal Ocean Observing Systems (NERACOOS) buoys. Data are from downcasts only, as the instrument was recovered quickly in order for the vessels to get underway. (a) Data collected by Bar Harbor Whale Watch on 7/11/2022 at 17:35 EST (Latitude 44.36447; Longitude –67.4664) compared with Station 44034 - Buoy I01 - Eastern Maine Shelf. (b) Data collected by Bar Harbor Whale Watch on 6/20/2022 at 17:13 EST (Latitude 44.060556 Longitude –68.320833) compared with Station 44034 - Buoy I01 - Eastern Maine Shelf. (c) Data collected by Bar Harbor Whale Watch on 8/16/2022 at 10:46 EST (Latitude 44.0749 Longitude –68.12229) compared with Station 44034 - Buoy I01 - Eastern Maine Shelf. (d) Data collected by Bar Harbor Whale Watch on 6/01/2022 at 17:05 EST (Latitude 44.12306 Longitude –67.20528) compared with Station 44034 - Buoy I01 - Eastern Maine Shelf. (e) Data collected by Bar Harbor Whale Watch on 8/10/2022 at 16:21 EST (Latitude 44.024444 Longitude –68.191667) compared with Station 44034 - Buoy I01 - Eastern Maine Shelf. (f) Data collected by Blue Ocean Society on 5/25/22 at 13:35 EST (Latitude 44.39529 Longitude –68.15472) compared with Station 44029 - Buoy A01 - Massachusetts Bay. > High res figure
|
Field Applications
The OpenCTD is designed and tested for depths of up to 140 m, which is suitable for most applications within the margins of a continental shelf or above the mesopelagic zone of the deep ocean. The OpenCTD sensor platform lacks the resolution of high-end commercial CTDs that can resolve temperature and salinity to hundredths or thousandths of degrees or practical salinity units. Thus, while the OpenCTD would not be appropriate for certain physical or chemical oceanography applications, it is more than adequate for ecology, conservation, and monitoring applications. OpenCTDs can be cast by hand, lowered on a rod and reel, deployed on an anchor line, attached to other equipment, or mounted on a fixed mooring for long-term monitoring projects. This deployment flexibility makes the OpenCTD especially versatile compared to CTDs built for specific use cases.
Compared to commercial CTDs, the low-cost sensors of the OpenCTD take longer to reach equilibrium. To maximize data quality, the speed at which the instrument is lowered should not exceed 1 meter per second (though slower is better when large temperature gradients are expected), with at least a minute long soak time at the surface to allow the sensors to reach equilibrium prior to descent. While the OpenCTD is useful in documenting clines in the ocean, it may be challenging to deploy in conditions where rapid changes in temperature or salinity are expected, such as at the entrance of a discharge pipe or the mouth of a glacial river, or where the speed of data collection is a priority.
Education and Outreach
The OpenCTD also functions as a STEM development platform, providing an intensive, project-focused experience for students interested in learning about environmental sensing. The OpenCTD Construction and Operation Manual has been written explicitly with a student audience in mind to facilitate easy integration into existing STEM syllabi. Successful OpenCTD building workshops have been conducted with high school and college students, graduate students, and professionals, and even with students as young as middle school.
Over the course of 2022, two intensive field programs were conducted using the OpenCTD. The Student Engineers Advancing Ocean Technology (SEAoTech) Program was conducted in partnership with the Bureau of Ocean Energy Management (BOEM), Education Passages, and the Center for Alaskan Coastal Studies. Middle and high school students from local schools in Homer, Alaska, constructed their own OpenCTDs and deployed them in Kachemak Bay to test hypotheses about oceanographic processes in their local waterways (Strobel, 2022).
In partnership with the National Marine Sanctuaries Foundation and BOEM, the Community Oceanography While Watching Whales program deployed prefabricated and calibrated OpenCTDs on commercial whale watching vessels. During regular cruises, naturalists aboard the whale watching boats performed CTD casts, providing an opportunity to educate their passengers while collecting high resolution oceanographic data at regular intervals in areas of environmental interest. Raw OpenCTD data, as well as photos of the deployment area, processed data, and water column profiles were made available via an ArcGIS Storymap (http://communityoceanography.com). Representative OpenCTD casts were compared against the nearest Northeastern Regional Association of Coastal Ocean Observing Systems (NERACOOS) buoys when available (Figure 3). Distance between representative OpenCTD casts and NERACOOS buoys ranged from a few kilometers to distances exceeding eighty kilometers.
Modifications and Future Development
The OpenCTD’s open platform allows users to modify the device to support a variety of sensors. The form factor of the control board allows direct one-to-one replacement of the conductivity probe with pH, dissolved oxygen, and reduction/oxidation potential systems produced by Atlas Scientific using drop-in source code for easy firmware updates. Other modifications that are being explored include: a channelized baseplate to increase water flow over the sensor package; larger batteries for long-term deployments; a solar charging circuit for fixed moorings; integration with open-source, 3D-printable Niskin bottles to create a fully open-source rosette; use of a commercial housing for swappable sensors; combining the OpenCTD with a camera for baited remote underwater video; and integration into a smart buoy system for real-time data collection. In one extreme case, the firmware and housing were heavily modified to create data loggers for the continuous monitoring of bioelectrical activity in a sediment microbial fuel cell array.
OpenCTD development is currently proceeding along two separate tracks. The education- and community-science-focused track uses the standard sensor configuration described here and includes curricula and other tools for teachers to integrate into STEM programs. The fieldwork-focused track aims to build a more robust OpenCTD with fewer DIY components, a smaller form factor, a more accurate P1000 temperature sensor and a 30-bar pressure sensor. The P1000 temperature sensor is a faster and more accurate module but requires a signal amplifier that introduces more noise and complexity to the system and is thus less forgiving for student workshop and DIY builds. This model will have a 300 m depth rating and provide data at a higher resolution than the standard model. While it will be released under the same open-source license, some custom components may have to be manufactured.
The introduction of any device or technology into marine ecosystems can present a potential hazard. Therefore, a set of guidelines for minimizing potentially harmful impacts when introducing new technologies into marine ecosystems was developed by individuals working in conservation technology and should be considered when deploying OpenCTDs (Thaler et al., 2015, 2019).
Conclusions
The OpenCTD offers an innovative, scalable technology for ocean monitoring and an alternative pathway for ocean knowledge seekers who need low-cost, accessible, reliable water metrology. As an education platform, the OpenCTD offers an opportunity for students to build and deploy their own oceanographic instruments and collect and analyze their own data. The open-source nature of the OpenCTD allows for expansion and adaptation, including the addition of new sensors into the existing housing as well as integration with other open-source systems. By enabling users to construct, calibrate, and maintain their own open-source instruments, the OpenCTD helps promote data independence and data autonomy, allowing knowledge seekers to take ownership of the production of knowledge essential to understanding our changing ocean.
Acknowledgments
Seed funding for the OpenCTD project was provided via a crowdfunding campaign to ADT and SKS via Rockethub. Sustaining funding for the OpenCTD was provided via an ongoing crowdfunding campaign to ADT via Patreon. The SEAoTech project was supported by a contract from the Bureau of Ocean Energy Management (140M0121D0004). Community Oceanography While Watching Whales was supported via a grant to ADT from the National Marine Sanctuaries Foundation and the Bureau of Ocean Energy Management (M17PG00019/P00002). A grant to improve the documentation for the project was provided by the Open-source Hardware Association to ADT.
Hundreds of individuals have contributed to making the OpenCTD program a success. The authors would like to acknowledge Ian Black, Kyle Worcester-Moore, Harold Tay, Jeff Branson, David Lang, Eric Stackpole, Walt Holm, the OpenROV/Sofar Ocean Team, Kim Martini, Miriam Goldstein, Alex Deghan and the Conservation X Labs Team, Cassie Stymiest of Educational Passages, the naturalists from Bar Harbor Whale Watch Company, Coastal Research & Education Society of Long Island, Boston Harbor City Cruises, Hyannis Whale Watch Cruises, Blue Ocean Society for Marine Conservation, and the College of the Atlantic, Henry Reiske and Katie Gavenus of the Center for Alaskan Coastal Studies, the students and teachers of Chapman School and Homer Flex High School in Alaska, Tammy Silva and David Wiley of the Stellwagen Bank National Marine Sanctuary, Brian Marx, Andrea Schmuttermair, Jamison Smith, Lisa Robbins, Ruth Stilwell, Allie Wilkinson, David Shiffman, and Amy Freitag.
Conflict of Interest
The authors received no compensation from any of the manufacturers used in the construction of the CTD. Thaler is the owner and CEO of Blackbeard Biologic: Science and Environmental Advisors, an environmental consulting firm that acts as the fiscal sponsor for the OpenCTD project.